Demand Controlled Ventilation Measurement Guide
Published: June 24, 2020
By: Phillip Chao, PhD | Applied Research Scientist, Peter Phung, Tom Lui | Interns, Duncan Prahl, RA, AIA | Sr. Applied Research Scientist
Reviewed by: Jillian Panagakos | Jr. Engineer, Honey Berk, LEED AP O&M,CMVP | Managing Director
Helpful Resources
Download this Guide
DownloadGeneral System Overview
This guide describes the measurement approach for quantifying energy savings associated with an air handling unit system retrofitted with a demand control ventilation (DCV) system. DCV is an energysaving strategy to maintain desired CO2 levels in a space based on occupancy. The types of AHUs addressed include:
- Constant Air Volume (CAV) with fixed discharge air temperature and a fixed damper position.
- Constant Air Volume (CAV) with fixed discharge air temperature and a variable OA damper position.
- Variable Air Volume (VAV) with fixed discharge air temperature and variable OA damper position.
Safety
This guide does not cover health and safety aspects of the collection of measurements at facilities. There are many hazards that exist in facilities surrounding the collection of measurements, including but not limited to: electrical safety, fall protection, personal protective equipment, control of hazardous energy (lock out/ tag out), confined space, respiratory protection, and machine safeguarding. Part of the measurement planning process must include the identification and mitigation of these and other hazards, and only qualified personnel should be used to support the implementation of a measurement strategy, as appropriate.
Description of System
The following sections provide background information on the components of an AHU and DCV. If you are already familiar with the system, you may skip to the Measurement Description for System section.
System Overview
An AHU provides conditioned air to the spaces it serves. This may include one or more of the following:
- Space heating/cooling
- Ventilation
- Humidification/Dehumidification
- Filtration
Depending on the size of the building, multiple AHUs will serve specific zones of the building.
The primary components of an AHU are listed below and shown in Figure 1.
- Supply/return fan maintains the air flow rate and pressure in the ductwork.
- Heating and cooling coils condition the supply air to a desired setpoint temperature.
- Dampers at the outdoor air intake, exhaust, and return air points control the amount of outdoor air, exhaust air, and return air in the AHU, respectively. Depending on ventilation requirements and the need to positively or negatively pressurize the building, some or all of the return air is mixed with the outdoor air.
- Filters remove particulates from the mixed air.
- Sensors and controls enable the operation of the AHU to meet specified comfort or outdoor air requirements. These may be standalone devices or integrated into a building automation system (BAS).
Various components of the AHU can be controlled to regulate operations and energy consumption. For example, fan motors may be retrofitted with VFDs to save energy by slowing the flow rate during unoccupied periods. Likewise, coil valves may be fitted with controllers to optimize heat transfer as heating/cooling loads vary.
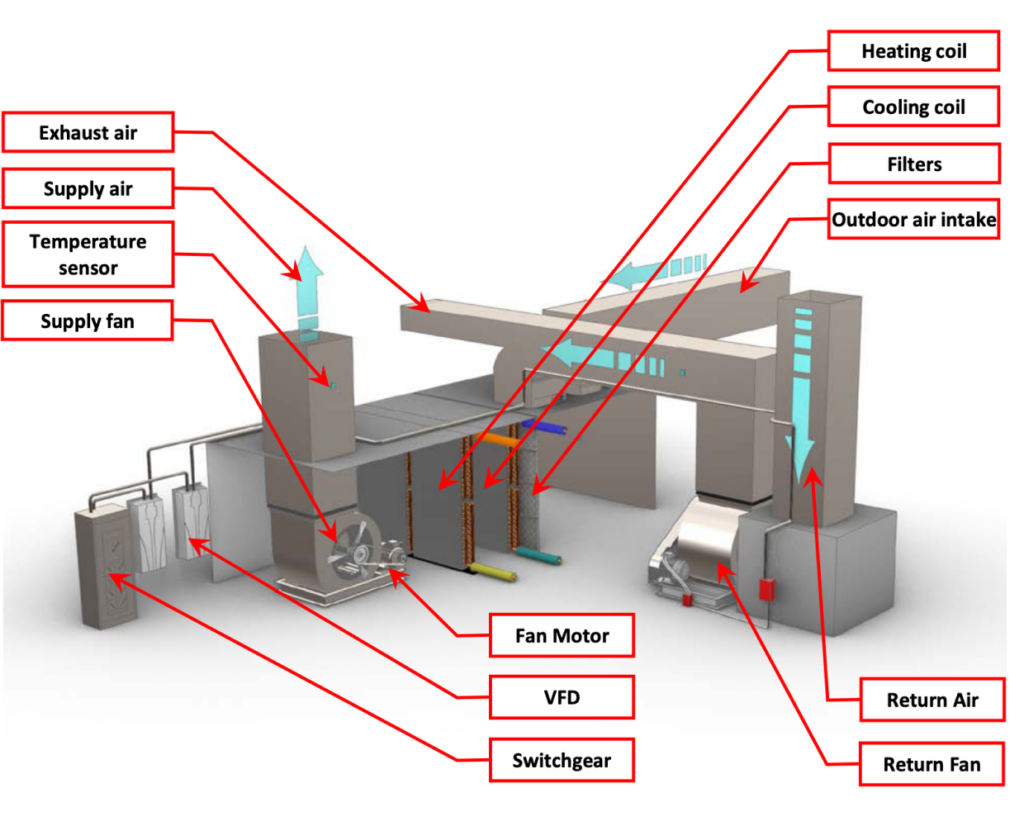
DCV saves energy in the AHU system by maintaining enough ventilation to meet occupant comfort needs when the zone is occupied, while minimizing ventilation when the zone is unoccupied. In a DCV system, some of the return air going to the AHU is mixed with fresh outdoor air supplied to the space, while the remainder is exhausted. DCV adjusts the volume of outdoor air to maintain a set CO2 level in the space. Figure 2, depicts a variable air volume, single-zone AHU system with DCV control. A CO2 sensor is installed in the return duct or in the conditioned air space. The controller modulates the damper motor actuators to open and close the outdoor, exhaust, and return air dampers proportionally to bring in enough outdoor air to maintain the desired CO2 level in the space. The VFD also modulates the fan speed based on the discharge air setpoint.
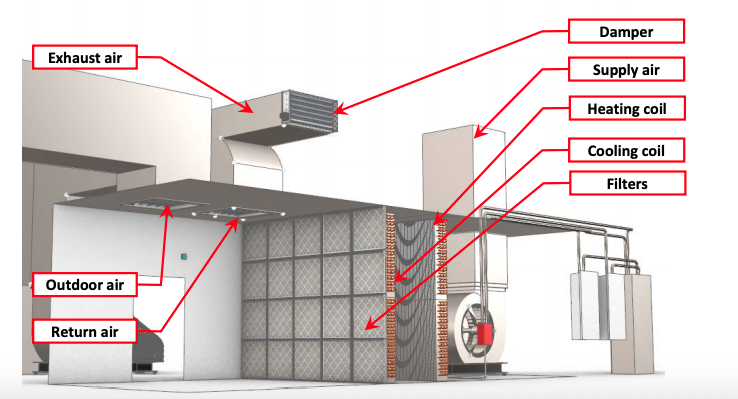
Key Variables Associated with Calculating Energy Consumption
The total energy used by the system is the sum of electrical energy used by the supply and return fan
motors and total heating and cooling energy used to heat or cool the air mass flowing through the AHU.
Fan Motor Energy: Electricity is used to power the AHU fan motor, which is measured in kWh. The
electricity consumption of an AHU fan motor is a function of the operating hours and the fan speed,
where the fan affinity laws define power as proportional to the cube of the fan speed. The relevant
variables used to characterize the electricity consumption of AHU fans are:
- True RMS power input to the VFD or motor for both supply and return fans.
- Operating Schedule including hours on or off and outdoor air volume required to maintain CO2 levels at any given hour.
- OAT (if fan speed or operation is OAT-dependent to supply heating or cooling).
While the electricity use of the motor is affected by the AHU design, operating rules, and cooling/heating loads, the goal of this guide is simply to assess avoided energy use, and hence no other variables are needed beyond the three listed above to measure fan energy electricity consumption.
Three common operational modes are covered in this guide:
The first mode is for a constant-speed motor, when no VFD has been installed. Electricity consumption (kWh) is the product of power draw (kW) and operating time (hours). The primary measurements, taken over several weeks, confirm the power draw and operating schedule.
The second mode assumes dual-speed operation based on the ventilation load and the supply air setpoint. In this case, measured data of hourly power draw is classified as either low- or high-speed power draw. The electricity consumption is then the high-speed power draw multiplied by operating hours at high speed plus the low-speed power draw multiplied by operating hours at low speed.
The third operating mode is a variable flow system where total system air flow and outdoor air flow varies with both OAT (as a proxy for heating and cooling loads) and CO2 levels. Hourly outdoor air volume is calculated using measurements of MAT, RAT, OAT, and AHU air flow, all correlated to a daily schedule by hour as a proxy for CO2 levels. True RMS power measurements for the fan are regressed with OAT to create a statistical model for OAT-dependent air flow. The annual electricity consumption is then the true RMS power (kW) drawn by the fan motor at a given OAT and CO2 level multiplied by the hours of operation of the fan at that given OAT and CO2 levels.
Heating and Cooling Energy: The total heating and cooling energy consumption is dependent on how much outdoor air is introduced as a result of the DCV operation. The total energy in the outdoor air as it enters the system is the latent heat carried by the air’s moisture and the sensible heat, as measured by the dry-bulb temperature. During cooling season, the cooling coils remove latent heat (through dehumidification) along with sensible heat. During heating season, it is assumed that only sensible heat is added by the heating coils, so changes in latent heat are minimal.
The necessary variables to assess the total heat and cooling energy are:
- Return, supply, mixed, and outside air temperatures
- Relative Humidity
- Supply Air flow
- Operating Schedule
- Boiler/Chiller efficiency
Supply air flow volume is assumed to be constant for a constant-volume system. While both boiler and chiller efficiency vary with operating conditions, constant values at average conditions are assumed. Interactive effects, such as decreased use of reheat coils, are ignored.
Operating Characteristics
AHUs manage air flow and temperature to meet heating, cooling, and ventilation demands. For a constant flow system, air flow is typically set to be constant, and heating or cooling coils are set to provide a specified discharge temperature for the supply air. Installation of a VFD allows for a reduction in air flow during unoccupied periods. Return fans are synchronized with supply fans to provide enough return pressure to maintain air flow through the AHU.
AHU systems are operated year-round, although operating rules differ between heating and cooling seasons. Ventilation requires a minimum air flow rate during occupied periods. If heating and cooling is not needed, the AHU could be shut down completely during unoccupied periods, provided the system has the capacity to re-establish desired indoor air temperatures after being turned off.
The DCV control system adjusts the percentage of outdoor air (outdoor air fraction, OAF) entering the AHU proportionally to CO2 level, which is a proxy for occupancy level. The outdoor air damper (OAD) has minimum and maximum setpoint positions corresponding to minimum and maximum CO2 levels, respectively. Furthermore, for VFD systems, the fan speeds are modulated to the minimum speed setpoint when CO2 levels are at their minimum, and vice versa for maximum CO2 levels. Since DCV control is part of the larger AHU control system, the DCV algorithm is overridden when economizing is suitable.
Scope of This Guide
This guide covers measurement strategies to estimate annual heating and cooling energy consumption for a single-zone AHU for several configurations – with or without DCV, and constant- or variable-flow AHUs. Measurement strategies to estimate annual electrical energy consumption are covered separately in the AHU Measurement Guide. These two measurement strategies should be conducted simultaneously to obtain an overall annual energy estimate. These annual estimates can be used to determine the annual avoided energy associated with changing from a pre-retrofit ventilation mode and OAD position to a post-retrofit DCV operating mode.
Constant-Speed, Constant-Volume AHU with Fixed Ventilation Rate: A constant-speed, constant volume, single-zone AHU with a fixed OAD position. This is the presumed typical pre-retrofit condition.
Constant-Speed, Constant-Volume AHU with DCV: A constant-speed, constant-volume, single-zone AHU with variable OAD position controlled by the DCV system. This is a simple, relatively low-cost DCV retrofit option with moderate energy savings potential.
AHU with Two Constant-Volume Air flows and DCV: A new two-speed motor provides two fixed volumes of air in the single-zone AHU with variable OAD position controlled by the DCV system. This is a simple, slightly more costly DCV retrofit option with a higher savings potential.
Variable-Speed, Variable-Volume AHU and DCV: A variable-speed, variable-volume, single-zone AHU with variable OAD position controlled by the DCV system. This is a more sophisticated and costly DCV retrofit option with the highest savings potential and the greatest flexibility for other operational improvements to the AHU.
For each mode, this guide describes the data that should be collected through measurements and the appropriate equipment to perform those measurements.
The guidance is for modular single-zone AHUs. AHU systems with airside economizer, multiple zones, single-packaged AHUs and RTUs (rooftop units) are not covered in this guide. Interactive effects with whole-facility heating and cooling loads due to the upgrade of the AHU fan motors (i.e., potentially lower cooling loads and higher heating loads due to less heat loss from the motor) are ignored.
If the fan motors are upgraded to VFDs as part of the DCV retrofit, then the appropriate pre- and post-retrofit measurement strategies should be chosen to accurately characterize the energy savings. Most likely, the pre-retrofit condition will be a constant-volume system with a fixed ventilation rate. The post-retrofit measurement strategy would be either the single- or two-speed air flows or the variable-volume air flow modes.
Frequently when a motor is replaced, other maintenance issues in the AHU are undertaken, such as coil cleaning, changing pulleys, or replacement of belts, all of which can impact total air flow. It is important to note these other operational changes and account for them as non-routine adjustments. This guide assumes that no maintenance is implemented in conjunction with the motor replacement, and that shaft RPM in the pre- and post-retrofit conditions is the same.
Measurements
This section begins with a description of the general measurement approach for heating and cooling energy estimates and concludes with the detailed steps required to perform the measurements. Please note that for electrical energy estimates, which are covered in the AHU Measurement Guide, supply and return fan power both need to be measured; while, for heating and cooling energy only supply fan power is needed (to calculate air flow rates). Therefore, the steps required to collect data for both supply and return fan power are described here, although only supply fan power is used to calculate heating and cooling energy.
Measurement Approach
This guide covers measurement strategies to estimate annual heating and cooling energy consumption for a single-zone AHU for several configurations – with or without DCV, and constant- or variable-flow AHUs.
Measuring Supply and Return Fan Power
True RMS power is measured at the power supply to the fan motors. As such, the measurement boundary is simply the fan motor plus the associated switchboard or VFD, as shown in Figure 3 and Figure 4, respectively.
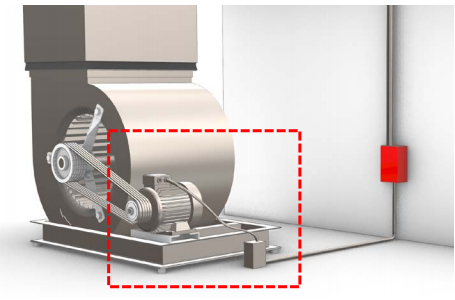
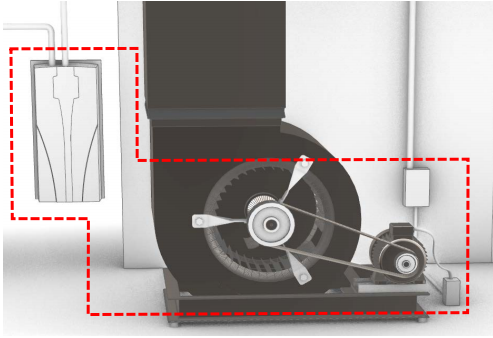
The measurement strategy for this system is determined by whether the fan is operated at a single speed or modulated with a VFD. Figure 5 illustrates a decision tree that can be used to identify which measurement strategy to apply to a specific system, based on its configuration and components.
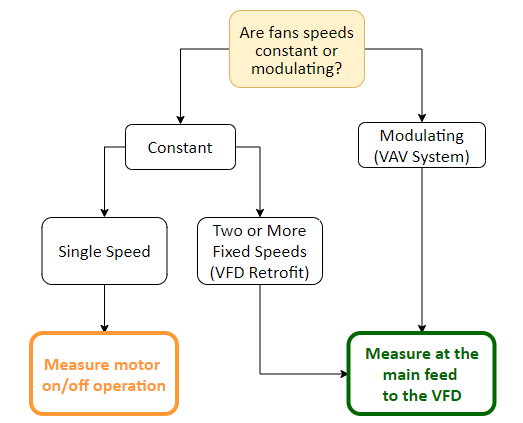
Measure Motor On/Off Operation
An AHU with a constant-speed fan is generally the pre-retrofit condition for most air handling units, and the post-retrofit condition when a constant-volume DCV system is retained or newly installed. This approach assumes that air flow remains relatively constant and the power draw stays constant throughout the measurement period. Because the motor operates at constant speed, it is either running at full power (when turned on) or it is drawing no power (when turned off). As such, a motor on/off data logger is used to track the operating schedule.
For both the supply and return fans, the following parameters should be measured:
- True RMS electrical power of the motor that drives the fan (kW)
- Fan motor runtime
If it is not possible to determine whether the fan motor has a constant power draw (e.g., through physical observation of the system, an interview with the building operator, or review of as-built drawings) it is best to derive runtime and power by using the next measurement strategy.
Measure at the Main Feed to the VFD
The measurement approach for two-speed or variable speed fans is the same – a direct or proxy measurement of power is needed to characterize the range of operation and how it varies with ventilation and OAT. Because fan power is proportional to the cube of the fan speed, it is important to measure fan power over the full range of load conditions. Several weeks of measurements backed up by documentation showing the programming in the controller is generally sufficient for two-speed fans. For fans equipped with VFDs, at least four-to-six weeks during the hottest time of summer, the coldest time of winter, and a few weeks during spring or fall should be sufficient to capture the operation of the system with respect to ventilation rate and OAT.
Measuring AHU Temperatures and Discharge Air Flow
To assess heating and cooling energy savings, the discharge air flow measurement and several temperature measurements are taken in the AHU. Figure 6 shows the measurement boundary and points.
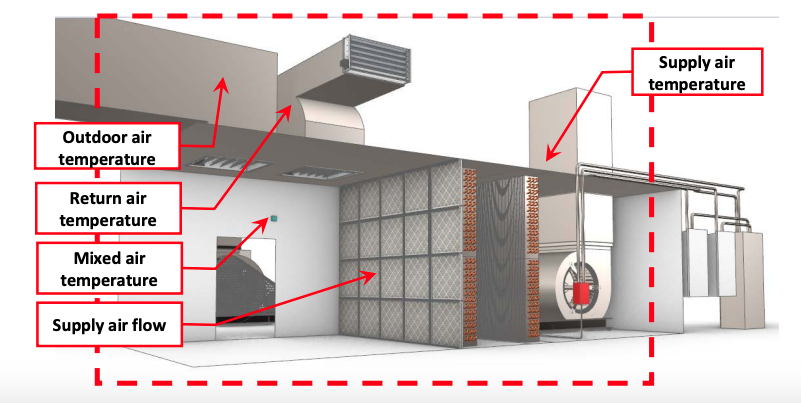
For both pre-retrofit and post-retrofit, the heat energy measurement approach is generally the same:
At least one gross air flow measurement of the discharge air flow from the AHU is needed. For constant air flow systems, the discharge air flow is assumed to be constant over time, regardless of OAD position. The air flow rate in a two-speed system is needed at both speeds. For fans equipped with VFDs that modulate across a range of speeds, the air flow and the corresponding power is needed across the range of speeds in order to construct a relationship between power and air flow.
One method to obtain the system air flow is from a test and balance report. For post-retrofit measurements, an air flow sensor can be included in the retrofit and the data can be downloaded from the DCV controller. A full duct transverse with a hot wire anemometer may be conducted to accurately measure the flow rate.
For variable-speed systems, if only one air flow measurement can be taken, it should be taken at the maximum flow and power levels. The fan affinity law can then be used to model air flow at lower measured power levels. Rather than the theoretical exponent of 3, a value of 2.5 is recommended, which is based on guidance from the Consortium for Energy Efficiency Guidebook for Industrial Efficiency Programs[5].
The outdoor, return, and mixed air temperatures provide a proxy for the volume of air being recirculated, exhausted, and brought in from the outdoors, the relative damper positions, and the CO2 levels in the space. Measuring these values over at least a four-week period will allow a characterization of how the DCV system operates for average occupancy patterns.
Sampling
If there are multiple units being upgraded in the building, it may be possible to sample them, provided they all have the same operating schedules. The following guidelines for sampling AHUs were developed by PNNL for the Building Re-tuning[2] protocol and are reasonable to apply to measurement of energy consumption:
- If there are fewer than six AHUs, then monitor all AHUs, otherwise measure about half of the AHUs.
- For tall buildings, measure at least one AHU per floor; for a particularly tall building, measure one AHU on every other floor.
- For buildings with occupied basements, include the basement AHU in the measurement plan.
If a more rigorous sampling plan is needed, Bonneville Power Administration[3] has developed an excellent resource for guidance.
Measurement Tools and Equipment
The measurements in this guide can be performed with the equipment listed in Table 1; more detailed descriptions have been provided in Table 2. NYC agency employees can borrow the recommended equipment from NYC Energy Tools, and have it delivered to their facility. Third-party M&V consultants and others can use this equipment list as guidance, recognizing that many manufacturers make comparable equipment. Inclusion on the list in Table 1 or Table 2 should not be construed as an endorsement of these manufacturers.
Measurement | Units | Tool | Equipment |
---|---|---|---|
True RMS Power | kW | Clamp Meter | Fluke 345 Power Quality Clamp Meter |
Apparent Current | Amperes | Current Sensor and Data Logger | Onset Split-Core AC Current Sensor (CTV-A, CTV-B or CTV-C) Onset HOBO 4-Channel Analog Data Logger (UX120-006M) |
True RMS Energy | kWh | Data-logging Power Meter and Current Transformers | DENT ELITEproXC Portable Power Data Logger (EXCUNC) Dent 16” RoCoil Flexible Rope Current Transformers (CT-R16-A4-U) |
Motor Runtime | Seconds / Hour | Motor On/Off Logger | Onset HOBO Motor On/Off Data Logger (UX90-004) |
OAT | °F | Weatherproof Temperature/Relative Humidity Data Logger | Onset HOBO Temperature/Relative Humidity Weatherproof Data Logger (MX2301) |
Air Flow | CFM | Hot Wire Anemometer | TSI-9545 Velocicalc Air Velocity Meter / TSI AVM430 Hot Wire Anemometer |
RT, MAT, DAT | °F | Temperature/Relative Humidity Data Logger | Temperature/Relative Humidity Data Logger (UX1101 or MX1101) |
Equipment | Description |
---|---|
![]() Fluke 345 Power Quality Clamp Meter | Multi-purpose electrical measurement tool used to take true RMS power readings over a short period of time. |
![]() Onset HOBO Split-Core Current Sensor | Provides a measurement of the current flowing through a conductor and converts to a signal the U12- or UX120-series data logger can record. Rated for specific amperage ranges – CTV-A 2-20 amps, CTV-B 5-50 amp or CTV-C 10-100 amp). Sensor should be selected based on the maximum or minimum amperage anticipated to be measured, to avoid out of range readings. |
![]() Onset HOBO 4-Channel Analog Data Logger (UX120-006M) | Used in conjunction with the CTV series of sensors. Records measurements from up to four CTV sensors. Requires HOBOware software and a USB connection cable for programming and downloading data files. |
![]() Onset HOBO Motor On/Off Data Logger (UX90-004) | Records when a motor is on and off, as well as runtime. Requires HOBOware software and a USB connection cable for programming and downloading data files. |
![]() DENT ELITEproXC Portable Power Data Logger (EXCUNC) ![]() DENT 16” RoCoil Flexible Rope Current Transformers (CT-R16-A4-U) | Provides a measurement of true RMS power from voltage and current inputs and records long-term power (kW) and energy (kWh) measurements. Requires ELOG19 software and a USB connection cable for programming and downloading data files. |
![]() Onset HOBO Temperature/Relative Humidity Weatherproof Data Logger (MX2301) | Records outdoor air temperature and relative humidity using internal sensors. Requires HOBOware software and a USB connection cable for programming and downloading data files. |
![]() TSI AVM 430 hot-wire-anemometer | Measures air flow, air velocity and temperature. A duct transverse must be conducted to get an average air flow across the full cross-section of the AHU. |
![]() temp-rh-logger-mx1101 | The UX1101 is a data logger which measures temperature and relative humidity with an internal sensor. MX1101 is the same data logger with Bluetooth capability, which allows for data downloads without having to open the AHU. |
Measurement Strategies
The following instructions have been developed for each measurement strategy discussed in this guide. While these are reasonably detailed, certain aspects of each strategy may need to be modified based on the specific system configuration at each facility. Early surveying of the facility is recommended when tailoring each strategy to unique site conditions.
The measurement recommendations reference supplementary equipment guides, which can be found in Appendix A.
A.1: Onset HOBO Motor On/Off Data Logger
A.2: Fluke 345 Clamp Meter
A.3: DENT ELITEpro XC Portable Power Data Logger
A.4: Onset HOBO 4 Channel Analog Logger and Onset Split-Core Current Sensor
A.6: Onset HOBO Outdoor Temperature and RH Data Logger
A.7: Onset HOBO Outdoor Temperature and RH Weatherproof Data Logger
A.10: TSI-9545 Velocicalc Air Velocity Meter /TSI AVM430 Hot Wire Anemometer
Supply and Return Fan Power Measurement Steps
There are three approaches to measuring the electrical power of the motors. The first two are for constant-speed systems, and the third is for variable-speed systems. In addition, an alternate approach is described for an AHU that has a BAS with data-trending capabilities.
Measure Motor On/Off Operation
This measurement approach is intended for constant speed, constant volume system configurations.
STEP 1: Preparation for Data Acquisition
- Confirm site conditions and locations where data acquisition equipment will be placed.
- Obtain measurement equipment from NYC Energy Tools:
- Onset HOBO Motor On/Off Data Logger (UX90-004)
- Fluke 345 Power Quality Clamp Meter
- Refer to A.1: Onset HOBO Motor On/Off Data Logger (UX-90-004)
- Set up and deploy data logger per the instructions in sections A.1.1 to A.1.3.
STEP 2: Installation at the Site
- Implement appropriate safety procedures.
- Refer to A.2: Fluke 345 Power Quality Clamp Meter
- Take a one-time measurement of true RMS power draw of the motor per the instructions in section A.2.1.
- Take a screenshot of the reading per the instructions in section A.2.2 (or, alternatively, a photograph using a cell phone).
- Refer to A.1: Onset HOBO Motor On/Off Data Logger (UX90-004)
- Install the motor on/off logger in the selected location and be sure the logger passes the ion with the motor running per the instructions in sections A.1.4 and A.1.5.
- Initial field setup is now complete.
STEP 3: Verify Data is Being Collected
- Implement appropriate safety procedures.
- If possible, wait for the first recording period to pass during the installation at site; if not, return to the site as soon as possible to retrieve data from the logger to verify data collection. Do not remove the logger from the equipment.
- Refer to Appendix A.1: Onset HOBO Motor On/Off Data Logger (UX90-004)
- Confirm that the logger is collecting data and that system operation is being recorded per the instructions in section A1.6. Be careful not to stop the logger when downloading data.
- It is recommended that this step be repeated periodically during the measurement period.
STEP 4: Retrieve Data Acquisition Equipment and Download Data
- Implement appropriate safety procedures.
- Refer to Appendix A.1: Onset HOBO Motor On/Off Data Logger (UX90-004)
- Confirm that the logger has collected the required operational data per the instructions in section A.1.6. Do not yet remove the logger from the equipment. Be careful not to stop the logger when downloading data.
- Once data acquisition has been confirmed, stop the logger per the instructions in section A.1.7.
- Remove the data logger and return to NYC Energy Tools.
Measure Power Consumed at Main Feed to Motor or VFD Using Data-logging Power Meter
This approach is the preferred method for a variable speed system (i.e., either two-speed or modulating with OAT), in which case a data-logging power meter (e.g., DENT ELITEproXC Portable Power Data Logger) is attached at the feed to the VFD. It can also be used for a constant speed, constant volume system configuration, in which case the measurement should be taken at the motor switch panel.
STEP 1: Preparation for Data Acquisition
- Confirm site conditions and locations where data acquisition equipment will be placed.
- For a single- or two-speed system:
- Obtain measurement equipment from NYC Energy Tools:
- DENT ELITEproXC Portable Power Data Logger – (EXCUNC) with 16” Flexible Current Transformers (CTs) (DENT CT-R16-A4-U)
- Obtain measurement equipment from NYC Energy Tools:
- Refer to Appendix A.3: DENT ELITEproXC Portable Power Data Logger
- Set up and initialize the DENT logger per the instructions in section A.3.1.
- For a continuously variable system with OAT:
- Obtain measurement equipment from NYC Energy Tools:
- DENT ELITEproXC Portable Power Data Logger– (EXCUNC) with 16” Flexible CTs (DENT CT-R16-A4-U)
- If the AHU varies air volume based on OAT, also use the Onset HOBO Temperature/Relative Humidity Weatherproof Data Logger (MX2301)
- Obtain measurement equipment from NYC Energy Tools:
- Refer to Appendix A.3: DENT ELITEproXC Portable Power Data Logger
- Set up and initialize the DENT logger per the instructions in sections A.3.1.
- Refer to Appendix A.7: Onset HOBO Temperature/Relative Humidity Weatherproof Data Logger (MX2301)
- Set up and initialize the Temperature/Relative Humidity Weatherproof Data Logger, per the instructions in sections A.7.1 through A.7.3.
STEP 2: Installation at the Site
- Implement appropriate safety procedures.
- For a single or two-speed system refer to Appendix A.3: DENT ELITEproXC Portable Power Data Logger
- Install the DENT ELITEproXC Portable Power Data Logger using sections A.3.2 to A.3.3 as guidance.
- For a continuously variable system with OAT refer to Appendix A.3: DENT ELITEproXC Portable Power Data Logger and Appendix A.7: Onset HOBO Temperature/Relative Humidity Weatherproof Logger (MX2301)
- Install the DENT ELITEproXC Portable Power Data Logger using sections A.3.2 to A.3.3 as guidance.
- Install the Temperature/Relative Humidity Weatherproof Data Logger using section A.7.4 as guidance.
- Initial field setup is now complete.
STEP 3: Verify Data is Being Collected
- Implement appropriate safety procedures.
- If possible, wait for the first recording period to pass during the installation at site; if not, return to the site as soon as possible to retrieve data from the logger to verify data collection. Do not remove the logger from the equipment.
- For a single or two-speed system refer to Appendix A.3: DENT ELITEproXC Portable Power Data Logger
- Confirm that the DENT ELITEproXC Portable Power Data Logger is collecting data and that system operation is being recorded per the instructions in section A.3.4. Be careful not to stop the meter when downloading data.
- For a continuously variable system with OAT refer to Appendix A.3: DENT ELITEproXC Portable Power Data Logger and Appendix A.7: Onset HOBO Temperature/Relative Humidity Weatherproof Logger (MXX2301)
- Confirm that the DENT ELITEproXC Portable Power Data Logger and Onset HOBO Temperature/Relative Humidity Weatherproof Data Logger (MX2301) are collecting data and that system operation is being recorded per the instructions in sections A.3.4 and A.7.5, respectively. Be careful not to stop the loggers when downloading data.
- It is recommended that this step be repeated periodically during the measurement period.
STEP 4: Retrieve Data Acquisition Equipment and Download Data
- Implement appropriate safety procedures.
- For a single or two-speed system refer to Appendix A.3: DENT ELITEproXC Portable Power Data Logger
- Confirm that the DENT ELITEproXC Portable Power Data Logger has collected the required data per the instructions in section A.3.4. Do not yet remove the meter from the equipment. Be careful not to stop the meter when downloading data.
- Once data acquisition has been confirmed, stop the logger per the instructions in section A.3.5.
- For a continuously variable system with OAT refer to Appendix A.3: DENT ELITEproXC Portable Power Data Logger and Appendix A.7: Onset HOBO Temperature/Relative Humidity Weatherproof Logger (MX2301)
- Confirm that the DENT ELITEproXC Portable Power Data Logger and Temperature/Relative Humidity Weatherproof Data Logger have both collected the required data per the instructions in sections A.3.4 and A.7.5, respectively. Do not yet remove the loggers from the equipment. Be careful not to stop the loggers when downloading data.
- Once data acquisition has been confirmed, stop the loggers per the instructions in section A.3.5 and A.7.6, respectively.
- Remove the data logger and return to NYC Energy Tools.
Measure Current Supplied to Motor at Main Feed to VFD Using Current Sensor
This measurement approach is intended as an alternative method for a two-speed or variable-speed VFD system. It can also be used for a constant-speed, constant-volume system configuration where the measurement is taken at the switchgear instead of at the VFD.
If the DENT ELITEproXC Portable Power Data Logger (or equivalent) is not available or cannot be installed due to space or other constraints, an alternative is to:
- Ask the facility representative to set the motor to run at the low speed setting. Take one-time true RMS power, voltage, apparent current and power factor measurements with a Fluke 345 Power Quality Clamp Meter (or equivalent). Repeat at the high speed setting.
- Record the long-term apparent current being drawn by the motor with a current sensor and analog data logger on one or all of the conductors that serve the motor.
STEP 1: Preparation for Data Acquisition
- Confirm site conditions and locations where data acquisition equipment will be placed.
- Obtain measurement equipment from NYC Energy Tools:
- Fluke 345 Power Quality Clamp Meter
- Onset HOBO 4-Channel Analog Logger (UX120-006M)
- Onset HOBO Split-Core Current Sensor (CTV-A, B or C)
- Refer to Appendix A.4 Onset HOBO 4-Channel Analog Logger (UX120-006M) with Onset HOBO Split-Core Current Sensor setup, install and Data collection
- Set up and deploy data logger per the instructions in sections A.4.1 to A.4.3.
STEP 2: Installation at the Site
- Implement appropriate safety procedures.
- Refer to Appendix A.4 Onset HOBO 4-Channel Analog Logger (UX120-006M) with Onset HOBO Split-Core Current Sensor setup, install, and Data Collection
- Install the current sensors and analog logger using section A.4.4 as guidance.
- Working with the appropriate facility personnel, measure the VFD when set to both low and high speeds.
- For each speed of the VFD, refer to Appendix A.2: Fluke 345 Power Quality Clamp Meter
- Take a one-time measurement of true RMS power draw of the motor, apparent current, power factor, and voltage per the instructions in section A.2.1.
- Take a screenshot of the reading per the instructions in section A.2.2 (or, alternatively, a photograph using a cell phone).
- If the fan is constant speed and constant volume, only one true power reading is needed.
- For each speed of the VFD, refer to Appendix A.2: Fluke 345 Power Quality Clamp Meter
- Initial field setup is now complete.
STEP 3: Verify Data is Being Collected
- Implement appropriate safety procedures.
- If possible, wait for the first recording period to pass during the installation at site; if not, return to the site as soon as possible to retrieve data from the logger to verify data collection. Do not remove the logger from the equipment.
- Refer to Appendix A.4 Onset HOBO 4-Channel Analog Logger (UX0-006M) with Onset HOBO Split-Core Current Sensor Setup, Install and Data Collection
- Confirm that the logger is collecting data and that system operation is being recorded per the instructions in section A.4.5. Be careful not to stop the logger when downloading data.
- It is recommended that this step be repeated periodically during the measurement period.
STEP 4: Retrieve Data Acquisition Equipment and Download Data
- Implement appropriate safety procedures.
- Refer to Appendix A.4 Onset HOBO 4-Channel Analog Logger (UX120-006M) with Onset HOBO Split-Core Current Sensor Setup, Install and Data Collection
- Confirm that the logger has collected the required operational data per the instructions in section A.4.5. Do not yet remove the logger from the equipment. Be careful not to stop the logger when downloading data.
- Once data acquisition has been confirmed, stop the logger per the instructions in section A.4.6.
- Remove the data logger and return to NYC Energy Tools.
Alternate Strategy: Download Data Directly from a BAS or VFD
This measurement approach is intended to be used for a two-speed VFD system that is controlled by a BAS or by a VFD with data-trending and exporting capability.
STEP 1: Preparation for Data Acquisition
- Confirm that the system can record either motor speed (in RPM) or percentage of full speed (in percentage). If possible, also record true RMS power. In lieu of true RMS power, current, voltage, and power factor may still be available. In this case, true RMS power can be calculated.
- Work with the installer to program the VFD to record hourly average RPM or percent of full speed, as well was true RMS power (where possible).
- If the system cannot record true RMS power, obtain the following from NYC Energy Tools:
- Fluke 345 Power Quality Clamp Meter
STEP 2: Installation at the Site
- Note that, for this measurement approach, installation at the site will only be required if the system cannot record true RMS power.
- Implement appropriate safety procedures.
- Working with the appropriate facility personnel, ramp the VFD to various speeds at which the VFD is programmed to operate.
- For each speed of the VFD, refer to Appendix A.2: Fluke Power Quality 345 Clamp Meter
- Take a one-time measurement of true RMS power draw of the motor, apparent current, power factor, and voltage per the instructions in section A.2.1.
- Take a screenshot of the reading per the instructions in section A.2.2. (or, alternatively, a photograph using a cell phone).
- For each speed of the VFD, refer to Appendix A.2: Fluke Power Quality 345 Clamp Meter
- Initial field setup is now complete.
STEP 3: Verify Data is Being Collected
- Implement appropriate safety procedures.
- If possible, wait for the first recording period to pass during the installation at site; if not, return to the site as soon as possible to retrieve data from the system. Do not stop the data recording process when downloading the data.
- Confirm that the data is being collected in the proper format, as required by the calculation spreadsheet.
- It is recommended that this step be repeated periodically during the measurement period.
STEP 4: Retrieve Data Acquisition Equipment and Download Data
- Implement appropriate safety procedures.
- Download data from the system for the duration of the measurement period.
- Format the data into a Microsoft Excel spreadsheet in the appropriate format for the calculation spreadsheet.
AHU Temperature and Air Flow Measurement Steps
Regardless of whether the measurement is for the heating or cooling season, both air flow and AHU temperatures (RAT, OAT, MAT, and DAT) must be measured. For a constant-speed system, a single air flow measurement is needed. For all other systems, a relationship between air flow and fan power needs to be established. A test and balance report may have the gross system air flow at high speed. An alternative approach, at least for post-retrofit measurement, is to have an air flow sensor included in the retrofit and trending capability programmed into the controller so the data can be recorded and downloaded. Based on the system configuration, a full duct transverse with a hot wire anemometer may be conducted to accurately measure the flow rate.
AHU temperatures are measured over a period of at least four weeks to characterize how DCV controls OAD position. In addition, an alternate approach is described for an AHU that has a BAS with data trending capabilities.
Measure Air Flow
For constant-speed fans, one duct transverse along with a spot measurement of fan power is needed. For variable speed fans, ideally four duct transverses along with spot measurement of fan power at four speeds (100%, 75%, 50%, and 25% of max speed) is needed. If it is not feasible to conduct four duct transverses, then one duct transverse at the top speed is acceptable and the flow at different speeds can be modeled with the fan affinity law.
STEP 1: Preparation for Data Acquisition
- Confirm site conditions and locations where data acquisition equipment will be placed.
- Obtain measurement equipment from NYC Energy Tools:
- Hot Wire Anemometer (AVM430)
- Fluke 345 Power Quality Clamp Meter (Fluke 345)
- Refer to Appendix A.10 Hot Wire Anemometer
- Set up and deploy the sensor and data logger per the instructions in sections A.10.1 to A.10.2.
STEP 2: Installation at the Site
- Implement appropriate safety procedures.
- Working with the appropriate facility personnel.
- Determine where on the AHU to conduct the duct transverse.
- Conduct the duct transverse per instructions in section A.10.3.
- Refer to A.2: Fluke 345 Clamp Meter
- Take a one-time measurement of true RMS power draw of the motor per the instructions in section A.2.1
- Repeat if possible, for variable speed systems at 100%, 75%, 50%, and 25% of the max speed.
STEP 3: Retrieve Data Acquisition Equipment and Download Data
- Implement appropriate safety procedures.
- Refer to Appendix A.10 Hot Wire Anemometer
- Download the data from the Hot Wire Anemometer per A.10.4.
- Return the Hot Wire Anemometer and Clamp Meter to NYC Energy Tools.
Measure AHU Temperatures
STEP 1: Preparation for Data Acquisition
- Confirm site conditions and locations where data acquisition equipment will be placed.
- Obtain measurement equipment from NYC Energy Tools:
- Onset HOBO Temperature/RH Weatherproof Data Logger (MX2301)
- Onset HOBO Temperature/RH Data Logger – (MX1101) (3 sets)
- Refer to Appendix A.6 Onset HOBO Temperature/RH Data Logger
- Set up and deploy the sensor and data logger per the instructions in sections A.6.1 to A.6.3.
- Refer to Appendix A.7 Onset HOBO Temperature/RH Weatherproof Data Logger
- Set up and deploy data logger per the instructions in sections A.7.1 to A.7.3.
STEP 2: Installation at the Site
- Implement appropriate safety procedures.
- Working with the appropriate facility personnel, access the AHU to position the three sets of temperature loggers and sensors at for RAT, MAT, SAT measurement.
- Refer to Appendix A.6 Onset HOBO Temperature/RH Data Logger
- Install the sensors and data logger using section A.6.1 to A.6.3 as guidance.
- Working with the appropriate facility personnel, access the AHU to position Temperature/RH Data Logger for OAT measurement.
- Refer to Appendix A.7 Onset HOBO Temperature/RH Weatherproof Data Logger
- Install the data logger using section A.7.4 as guidance.
STEP 3: Verify Data is Being Collected
- Implement appropriate safety procedures.
- If possible, wait for the first recording period to pass during the installation at site; if not, return to the site as soon as possible to retrieve data from the logger to verify data collection. Do not remove the logger from the equipment.
- Refer to Appendix A.6 Onset HOBO Temperature/RH Data Logger
- Confirm that the logger is collecting data and that system operation is being recorded per the instructions in section A.6.5. Be careful not to stop the logger when downloading data.
- Refer to Appendix A.7 Onset HOBO Temperature/RH Weatherproof Data Logger
- Confirm that the logger is collecting data and that system operation is being recorded per the instructions in section A.7.5. Be careful not to stop the logger when downloading data.
- It is recommended that this step be repeated periodically during the measurement period.
STEP 4: Retrieve Data Acquisition Equipment and Download Data
- Implement appropriate safety procedures.
- Refer to Appendix A.6 Onset HOBO Temperature/RH Data Logger
- Confirm that the logger has collected the required operational data per the instructions in section A.6.5 Do not yet remove the logger from the equipment. Be careful not to stop the logger when downloading data.
- Once data acquisition has been confirmed, stop the logger per the instructions in section A__
- Refer to Appendix A.7 Onset HOBO Temperature/RH Weatherproof Data Logger
- Confirm that the logger has collected the required operational data per the instructions in section A.7.5 Do not yet remove the logger from the equipment. Be careful not to stop the logger when downloading data.
- Once data acquisition has been confirmed, stop the logger per the instructions in section A.7.5
- Remove the data loggers and sensors and return them to NYC Energy Tools.
Calculation Methodology
General
The measurement strategies and calculations in this guide have been derived from several sources, including:
- ASHRAE Guideline 14: Measurement of Energy, Demand, and Water Savings[4]
- US Department of Energy’s Uniform Methods Project[5]
- Bonneville Power Authority’s Implementation Manual Document Library[6]
- EVO IPMVP Application Guides Family[7]
To adhere to the fundamental concepts discussed in this guide (appropriate, necessary, reasonable, replicable, consistent, simple, and purpose-driven) these strategies have been generalized to enable the broadest use possible. It should be noted that there are many situations where these strategies and the associated calculations will need to be modified to suit individual facilities or specific system configurations. Consult the above sources for additional detail and guidance on extrapolating these general guidelines to suit your specific situation.
The annual energy consumption of an AHU with DCV system includes both the electricity needed to run the fans and the thermal energy used by the AHU coils to either heat or cool the air. Four configurations are included in this guide:
- Configuration 1: Constant-Speed AHU Fan with Fixed OAD position
- Configuration 2: Constant-Speed AHU Fan with Variable OAD position
- Configuration 3: Dual-Speed AHU Fan with Variable OAD position
- Configuration 4: Continuously Variable-Speed AHU Fan with Variable OAD position
The calculation methodology for determining the annual electricity consumption of constant, dual speed, or continuously variable AHU fans is addressed under the AHU Measurement Guide. Please refer to that document for details on the calculations involved. Five Microsoft Excel workbooks have been developed to determine the annual electricity consumption for an AHU fan system:
- 2020_0512_ahu_fan_cscv_2speed_current_v1.xlsx (Configuration 3)
- 2020_0512_ahu_fan_2_speed_rpm_v1.xlsx (Configuration 3)
- 2020_0512_ahu_fan cscv_on_off_v1.xlsx (Configurations 1 and 2)
- 2020_0512_ahu_fan_cscv_1_speed_kwh_v1.xlsx (Configurations 1 and 2)
- 2020_0512_ahu_fan_var_volm_v1.xlsx (Configuration 4)
Three sets of Microsoft Excel workbooks have been developed along with this guide to facilitate the calculation of total annual heating and cooling energy consumption from the measured data. Each workbook consists of two calculation approaches: one for the cooling season and the other for the heating season.
Workbook Set 1:
- 20200618_Const Cooling DCV_Single Zone.xlsx (Configuration 1 and 2: Constant-Speed AHU Fan with Fixed OAD position or Variable OAD position)
- 20200618_Const Heating DCV_Single Zone.xlsx (Configuration 1 and 2: Constant-Speed AHU Fan with Fixed OAD position or Variable OAD position)
These workbooks are for AHUs with constant-speed and constant-volume fans. Measured input time series data includes DAT, MAT, RAT, OAT, and supply fan motor operational time per hour, as measured by a motor on/off logger. One-time measurement of the supply air flow in the AHU is also required as an input.
Workbook Set 2:
- 20200622_2_Speed_Cooling_DCV_Single Zone.xlsx (Configuration 3: Dual-Speed AHU Fan with Variable OAD position)
- 20200622_2_Speed_Heating DCV_Single Zone.xlsx (Configuration 3: Dual-Speed AHU Fan with Variable OAD position)
These workbooks are for dual-speed AHU fans. These workbooks use either current (in Amps) or motor speed (in rpm) as a proxy of operational time per hour for supply fans. The average hourly current (in Amps) is measured by a current sensor logger. The average hourly motor speed (in rpm) is collected from the VFD. One-time measurements for the supply air flow for supply fans operated at high speed and low speed in the AHU are needed as inputs.
Workbook Set 3:
- 20200629_Var_Cooling DCV_Single Zone.xlsx (Configuration 4: Continuously Variable-Speed AHU Fan with Variable OAD position)
- 20200629_Var_Heating DCV_Single Zone.xlsx (Configuration 4: Continuously Variable-Speed AHU Fan with Variable OAD position)
These workbooks are for a variable-volume AHU with variable-speed fans. These workbooks use the average hourly power draw (in kW), as measured by a data-logging power meter, as a proxy of operational time per hour for supply fans. The average hourly temperatures are measured by a temperature/RH logger. One-time measurement for the supply air flow over a range of fan speeds is needed as an input.
Instructions are included in each workbook that detail how to input data and how to interpret and make use of the results. Specific calculation methodologies can be found in Appendix A.13: AHU Fan Calculations and are captured in the workbooks.
Reporting Recommendations
As part of the documentation of expected avoided energy use, the integration of measurements and calculation methodology discussed in this guide will serve to enhance these projections. To facilitate transparency and data quality control, the following pieces of information should be documented to accompany expected savings calculations:
- Measurement tool information and dates of measurement. The HOBOware software records logger information (such as product, serial number, and version number) as well as deployment and measurement dates. To export this information, use the software to open the logger data file, then select “Export Details” from the File menu; this will produce a text file like the one shown in Figure 5. Repeat for all data loggers that were deployed and include all files with the funding application.
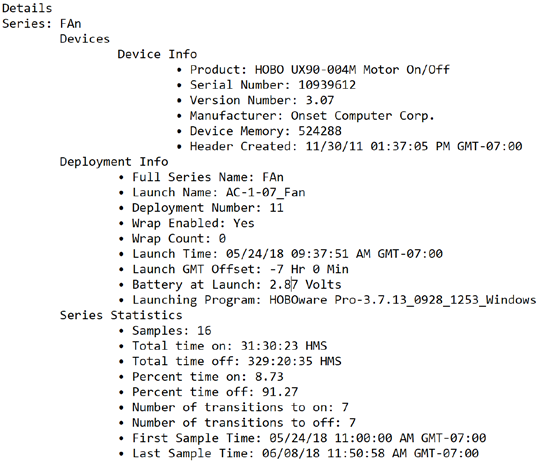
- If a BAS was used to collect any of the information discussed in this guide, submit a brief description of the system, including:
- BAS manufacturer and model
- BAS software and version number
- Measurement dates
- Most recent date of sensor calibration (if a sensor was used)
- The completed workbook(s) containing measured data.
It is expected that the user will be responsible for measuring the system of interest and compiling the data input to the calculation tools. The output of these tools can be directly used to satisfy reporting requirements.